最快每分钟一台车!“黑科技”加持的恒大工厂即将进入试产阶段
自从“六车齐发”,到车标、命名体系公布后,恒大汽车在不断加速自身节奏的步伐。在8月份曝光了广州和上海两家工厂后,日前再次迎来了重磅消息,这两家生产基地已完成设备安装调试,即将全面进入启动试生产调试阶段。
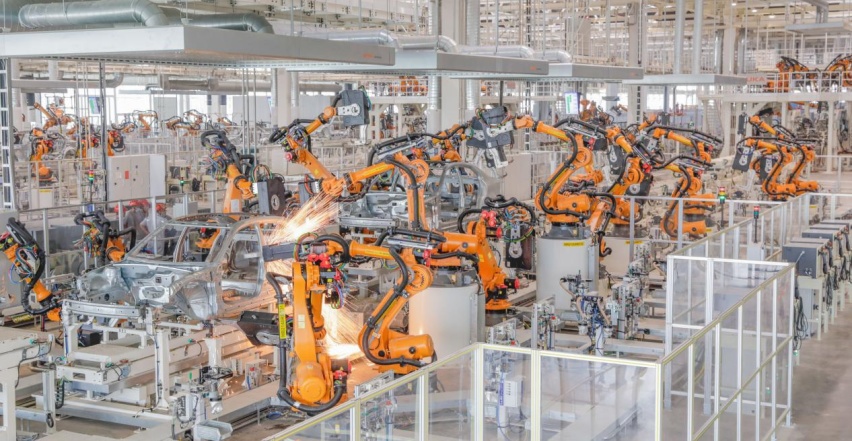
据了解,两大基地均按照工业4.0标准建设,配备一支机器人“造车天团”,由德国舒勒、库卡、杜尔、日本发那科等组成,共计2545台智能机器人,拥有世界最先进的装备、世界最先进的工艺,实现世界最先进的智能制造,全面达产后能做到每分钟生产1辆车。
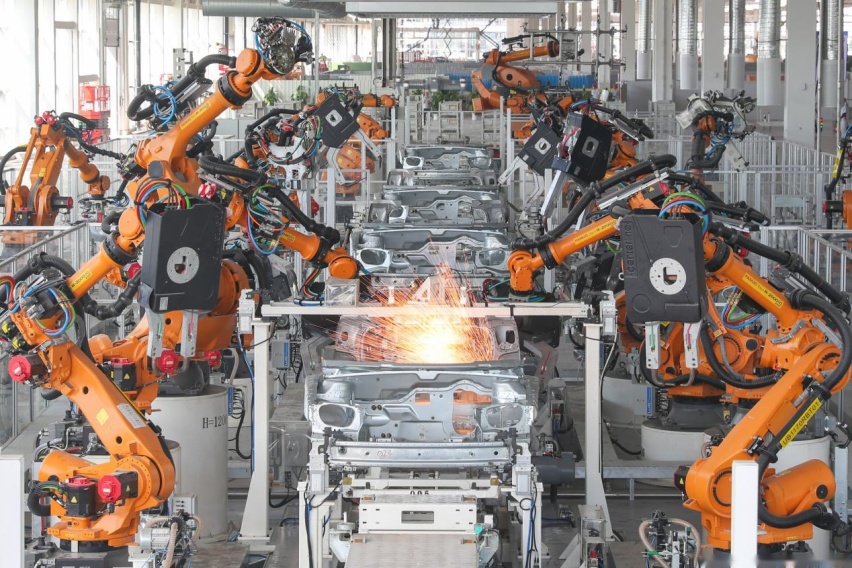
其次,四大车间均拥有世界最先进“黑科技”,以车身车间为例,通过德国库卡和日本发那科提供的顶级智能技术,可实现24小时不间断工作,成为了集成效率、智慧的高智能工厂。并且依托先进的技术加持,不仅在产能上得到提升,还保证了恒驰汽车的品质优势,而“黑灯”工作达到开源节流,可谓一举多得。
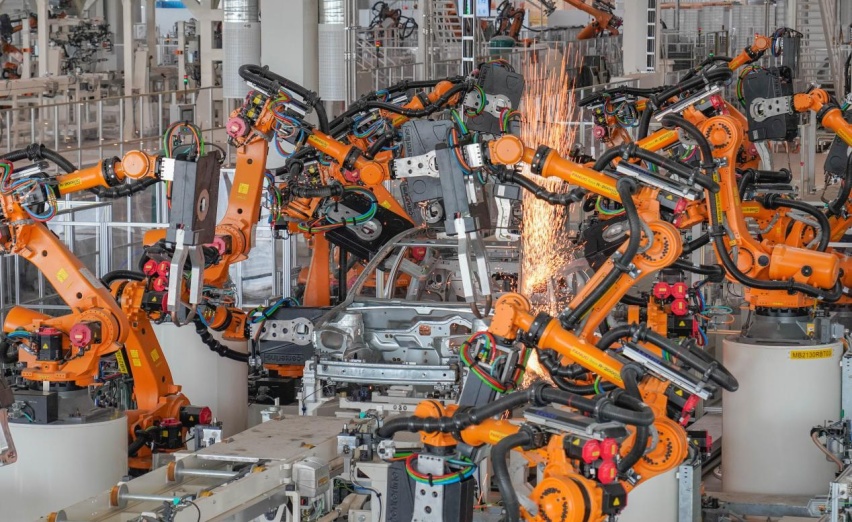
而每一个车间相互之间环环相扣,首先冲压车间采用的是德国舒勒冲压装备,其拥有MMS智能自诊断系统,能快速处理各种原材料,即使是一块钢板能迅速「变身」为车身形状,同时自身能够进行废料处理以及日常维护等功能,实现全自动冲压生产线。
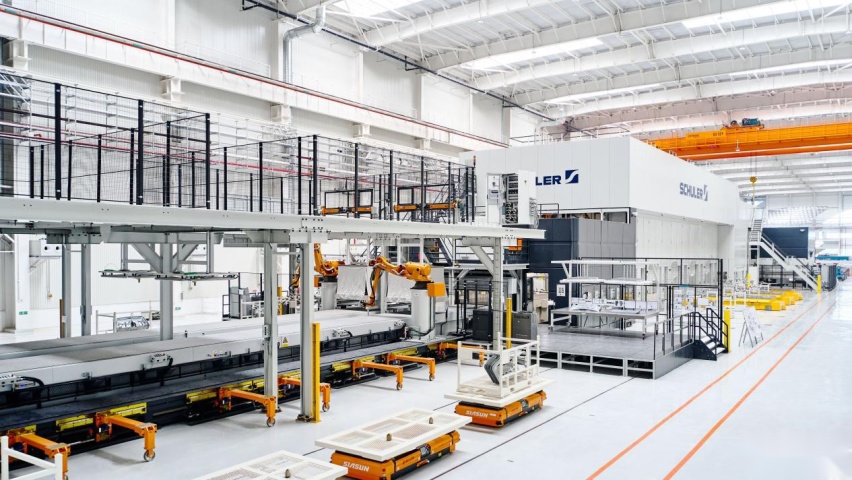
然后是车身车间,采用德国库卡和日本发那科装备,运用数字化双胞胎技术,打造出一副车间之间相互接通的大型网络架构,以智能科技 实现一体同步化。同时,德国库卡巨型机械臂可以长时间分毫不差地执行点焊、铆接、滚边、胶合等工作,实现24小时不间断工作,达到“黑灯工厂”的最终目的。
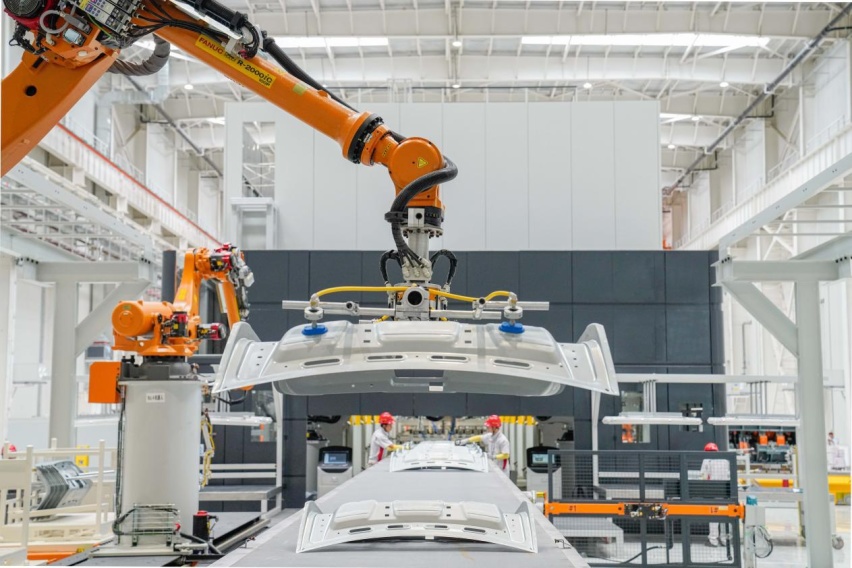
再来就是是涂装车间,采用德国的杜尔生产线,可实现全自动喷漆、涂胶,并引入横置烘炉、快速换色等技术,实现智能、环保、定制化涂装。其中手握3D喷枪的智能机器人能全方位、不留死角地完成自动喷漆、涂胶等任务,相比人工喷涂效率更加显著,色泽也更加均匀亮丽。
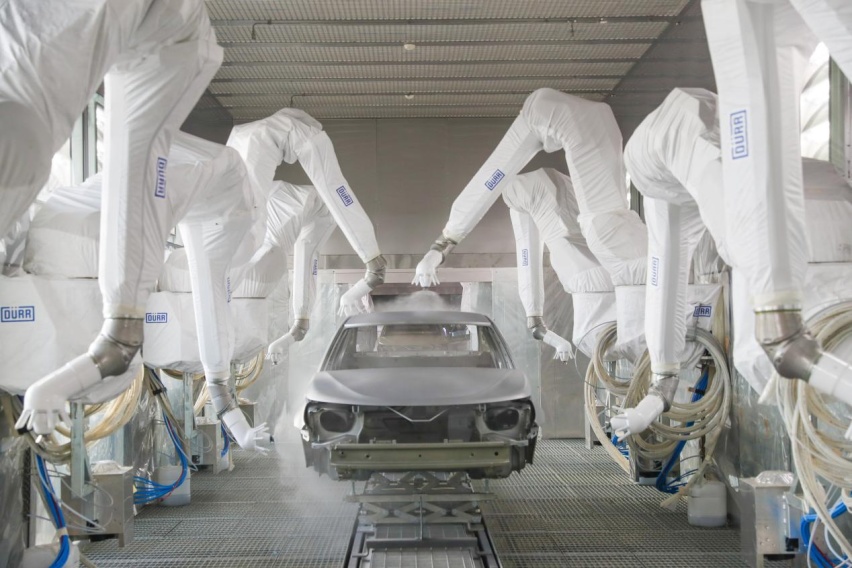
最后是装配车间,作为造车过程中的最后阶段,恒大采用德国杜尔全自动装配线,能够通过3D视觉定位系统,帮助机械臂快速精准地安装车门、车轮等重要零部件,有效降低劳动成本,同时保证了产品的装配质量,实现全智能高效一体化。
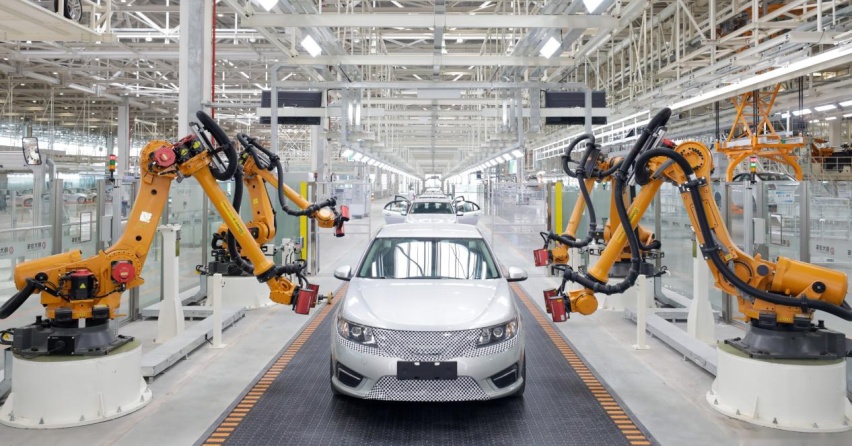
如此看来,一旦广州、上海工厂全面进入正式投产,配合全球多个生产基地,可在2025年前达到百万辆车型的生产目标,届时将一举成为全球具备最大规模以及实力的新能汽车集团。
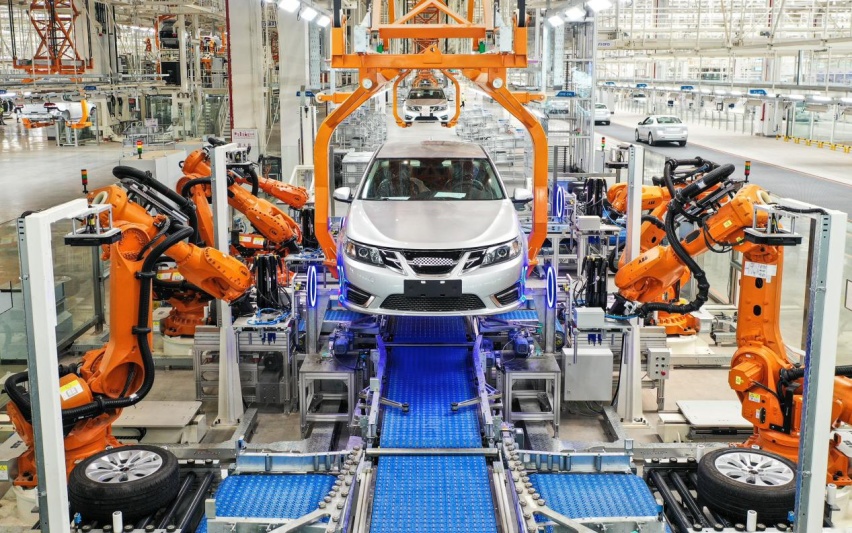
正如许家印先生所言:“我们要实现三到五年内,把恒大汽车打造成为世界规模最大、实力最强的新能源汽车集团,绝对不是梦!”。在经历众多事情后,恒大汽车逐渐步入正轨,拥有了最先进的智能制造基地,确保了产品品质和生产效率,这番说话所言不虚。