凭什么说ID.产品拥有高品质?探秘上汽大众新能源汽车工厂
不久前,上汽大众首款ID.纯电动车ID.4 X(参数|询价)正式亮相,这是一款基于大众全新纯电动平台——MEB平台打造的车型。如今电动车市场不再是新势力造车独占鳌头,传统车企也开始涉足纯电动车市场,相比之下,传统车企拥有更丰富的造车经验、更好的品牌影响力以及更广泛的销售渠道。传统车企的入局,使得纯电动车市场更具看点。
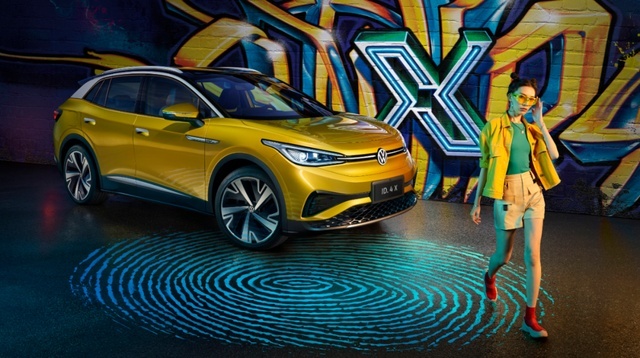
作为专门生产MEB平台车型的全新工厂,上汽大众新能源汽车工厂汇聚大量前沿制造技术,充分发挥企业的创新、技术与质量优势,为ID.家族产品注入高品质基因。该工厂规划年产能30万辆,是目前国内生产规模最大、效率最高的纯电动车工厂。工厂具备冲压、车身、油漆、总装和电池装配车间,拥有车体分配中心、自动化立体高架库、试车道等设施,是一座集智能制造、节能环保为一体的现代化标杆工厂。上汽大众也是对该工厂充满信心,为更好地证明ID.4 X的高品质,上汽大众为我们展示了新能源汽车工厂。
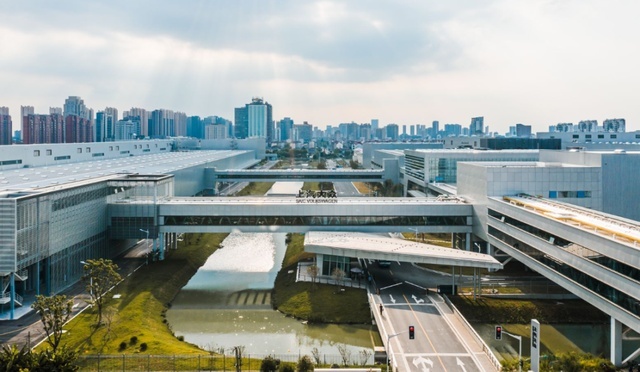
为保证MEB平台纯电动车大批量生产的品质稳定,上汽大众累计投入超170亿元,在上海投资建设了全球首个专门生产MEB平台纯电动车的工厂。该工厂代表了大众汽车集团最先进制造工艺,上汽大众投入了多项在企业、乃至大众汽车集团中首次使用的制造技术,全力保障ID.家族车型的生产效率及品质稳定。
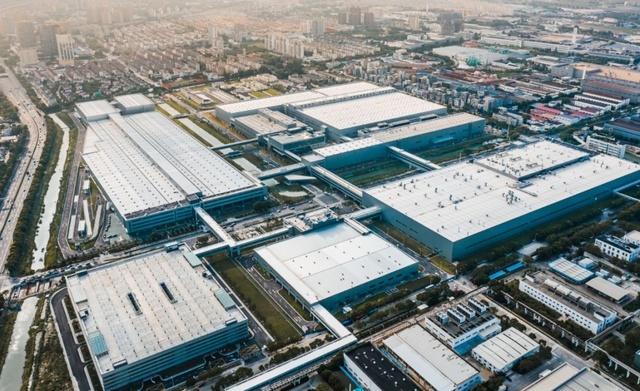
无人化全自动生产是上汽大众新能源汽车工厂的核心,据悉,整个工厂采用了超过1400台工业机器人,总装车间自动化率达到26.2%,相比传统总装车间提升近45%,而车身和电池车间基本实现无人化全自动生产。同时,为了提升生产稳定性,保障产品高质量,该工厂大量采用高度自动化装配和自动测量技术,投入自动拧紧、自动门板喷蜡、全自动仪表安装、全自动合装平台、空中输送线、AGV小车等多项新技术,在降低生产成本的同时也能提供更好的生产稳定性。
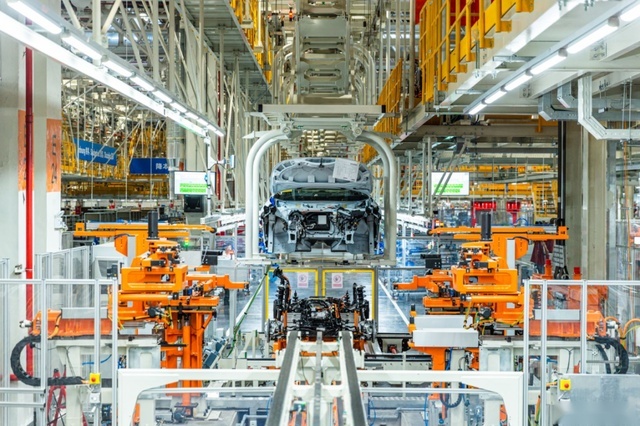
全自动合装平台
车身车间则是自动化率最高的生产车间,拥有机器人数量946台,自动化率高达84%。车身车间分2层结构,一楼主要是门盖 、底板1和装配线。二楼主要是侧围 、底板2、总拼以及报交线。车身车间的设计生产能力每小时可以完成60台白车身,年产量30万台。车身车间还首次应用了EMS空中输送存储线、机器人全自动拧紧工艺、冷金属过渡焊接等多项工艺。
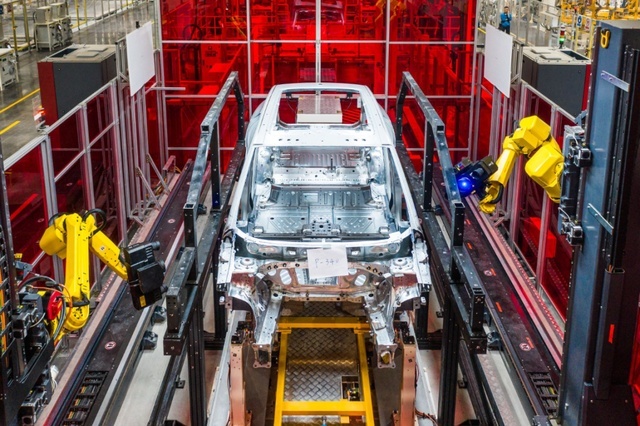
At-line测量工位
为最大程度保证白车身生产过程质量的稳定性,车间内设有两个大众汽车集团全球首次使用的At-line测量工位,其中8台测量机器人对白车身的零部件和关键部位实行100%的视觉在线检查,通过激光测量传感器、温度补偿、图像处理以及计算机控制等技术实现物体空间尺寸的精密测量,重复精度高达0.2mm。
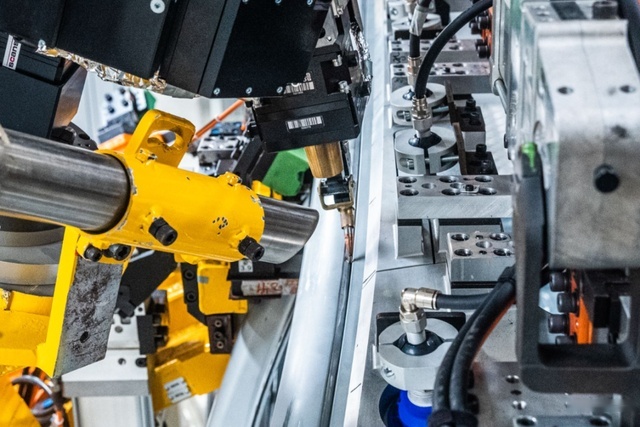
高速激光焊
值得一提的是,车身车间还采用了速度可达110mm/s的高速激光焊技术,这是大众汽车集团速度最快的激光焊,更好提升车身焊接质量与美观度。激光焊接技术具备高功率密度、优良的方向性和高焊接速度的优势,经过高速激光焊技术焊接之后,无需在车顶安装密封胶条;同时还可精确调节和控制热输入,镀锌层烧损更少,减小焊件的变形。该车间还拥有上汽大众最长的车间装配线,保证输送过程零件的一致性。
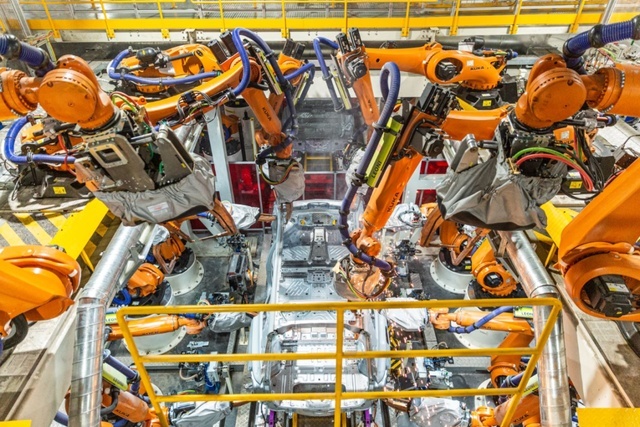
高密度焊接
在追求准确率与装配质量的总装车间中,上汽大众新能源汽车工厂首次使用全自动合装平台、全自动仪表安装、TDA车门头道密封等技术,该车间也成为目前大众汽车集团自动化率最高的量产车型总装车间,模块化程度和柔性更高。值得一提的是,该车间全自动仪表安装机械手的采用,大幅度地提高了效率以及准确率,是大众汽车集团全球首次应用的技术。
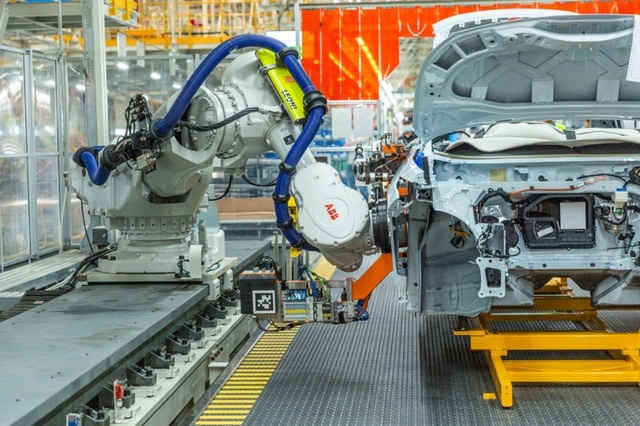
全自动仪表安装机械手
同时,总装车间还大量运用AGV小车,分别有物流AG及工艺AGV两种AGV小车运作。其中物流AGV,主要用于物流区向生产线工位运送物料;而工艺AGV,主要用于底盘预装工艺输送,和自动化安装工位高度融合。
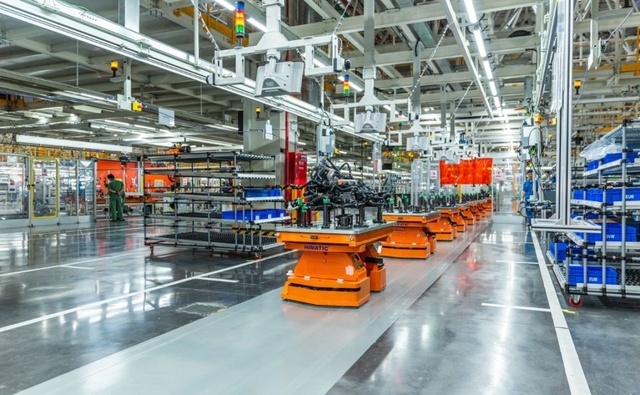
工艺AGV
上汽大众新能源汽车工厂也是全球首次应用TDA车门头道密封技术的工厂,该技术创新性地利用视觉识别来识别车门的偏移量,从而引导机器人自动取料、黏贴 、剪切、打孔。这不仅节省生产面积与工位,还改善了门关闭力和雨淋密封性能。
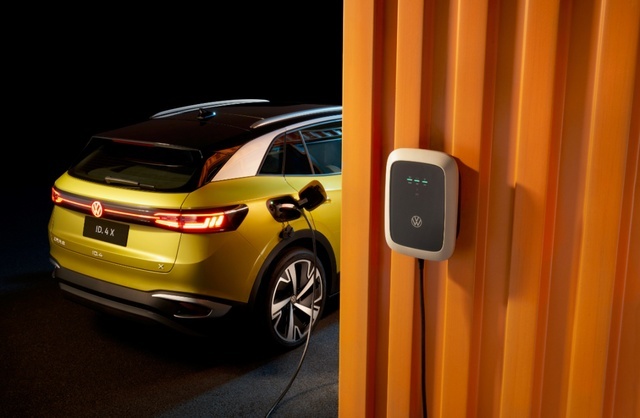
未来,该工厂可通过传感器物联网、移动互联网、大数据分析、人工智能等高新技术,使机械能按照人类思维模式相近的方式和既定的规则运作,通过数据处理和反馈不断学习,实现对随机性的外部环境做出判断,最终从生产效率、制造成本以及产品品质等方面逐步优化,以高度自动化、柔性化的生产为产品质量保驾护航,同时也为智能化升级奠定基础。
(图片来源网络,侵删)